Ob in der Industrie, im Handwerk oder im privaten Bereich – Schnellkupplungen ermöglichen es, Leitungen und Schläuche sekundenschnell zu verbinden und zu trennen, ohne Werkzeug oder hohen Kraftaufwand. Sie sind in Druckluftsystemen, Hydraulikanlagen, Kühlkreisläufen und vielen anderen technischen Bereichen unverzichtbar. Doch was macht eine hochwertige Lösung aus? Welche Mechanismen kommen zum Einsatz, und welche Materialien sind für bestimmte Anwendungen am besten geeignet? In diesem Artikel werfen wir einen detaillierten Blick auf die Technik hinter flexiblen Anschlüssen, erklären ihre Funktionsweise und zeigen, worauf es bei der Auswahl wirklich ankommt.
Präzise und schnell: Warum Verbindungstechnik zählt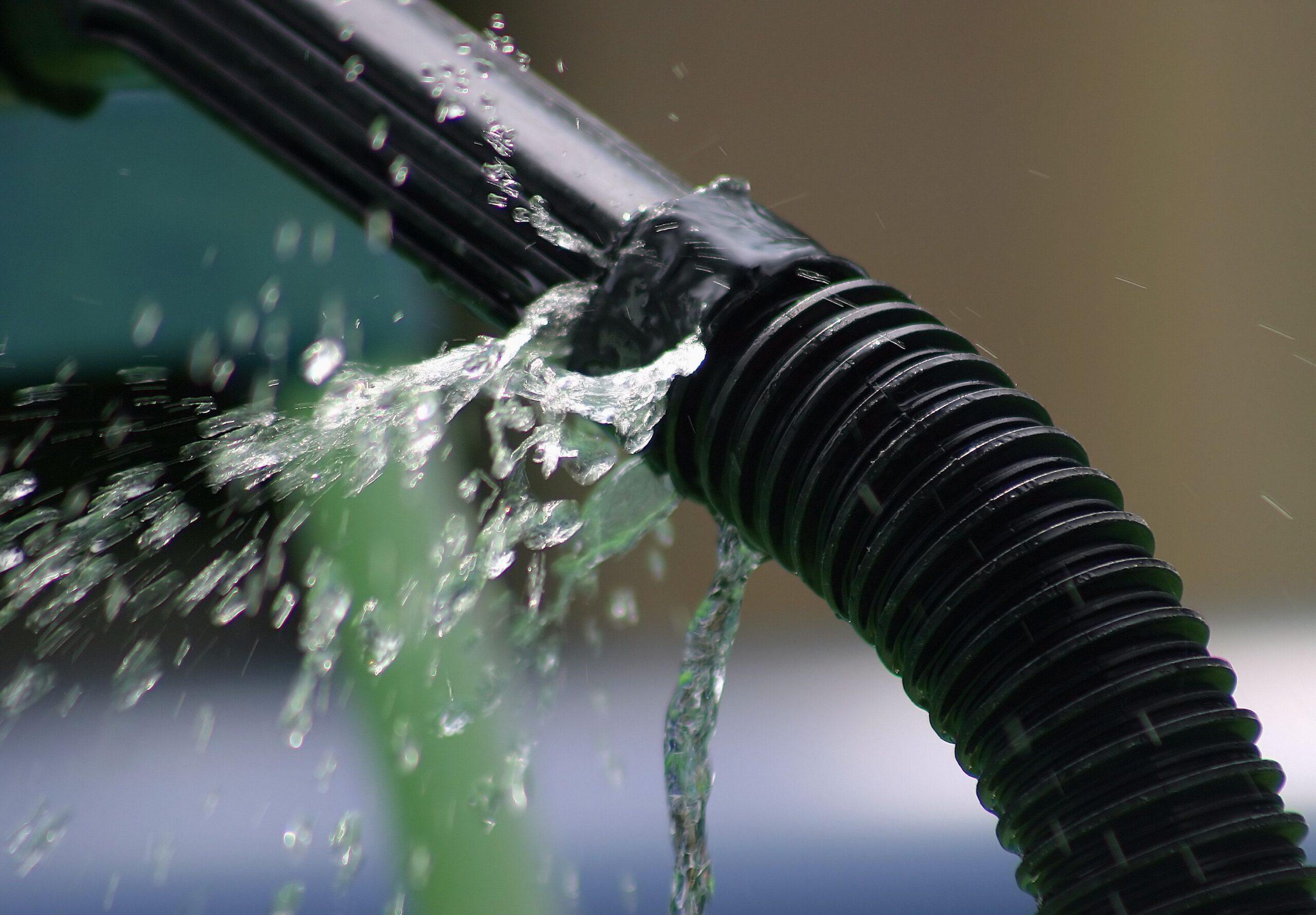
Die Bedeutung einer zuverlässigen Verbindungstechnik wird oft unterschätzt – bis Probleme auftreten. Undichte Systeme, ineffiziente Handhabung oder eine fehlerhafte Materialwahl können nicht nur zu Produktivitätsverlusten führen, sondern auch hohe Folgekosten nach sich ziehen. Gerade in sensiblen Bereichen wie der Medizintechnik oder der chemischen Industrie kann eine fehlerhafte Verbindung fatale Konsequenzen haben.
Ein effizientes Anschlusssystem muss daher mehrere Faktoren vereinen: Es sollte einfach und schnell zu bedienen sein, ohne an Sicherheit einzubüßen. Es muss widerstandsfähig gegenüber äußeren Einflüssen sein, beispielsweise extremen Temperaturen, Druckbelastungen oder chemischen Substanzen. Zudem spielt die Lebensdauer eine entscheidende Rolle – ein qualitativ hochwertiges Produkt amortisiert sich über die Jahre durch seine Langlebigkeit und Wartungsfreundlichkeit.
Auch die Ergonomie ist nicht zu vernachlässigen. Gerade in Arbeitsumgebungen, in denen häufig Anschlüsse getrennt und wiederhergestellt werden, kann eine intuitive Bedienung viel Zeit und Mühe sparen. Das Zusammenspiel all dieser Aspekte macht moderne Verbindungslösungen zu einem entscheidenden Faktor in vielen technischen und industriellen Prozessen.
Mechanik: Wie funktionieren flexible Verbindungssysteme?
Der Aufbau eines modernen Verbindungssystems ist auf maximale Funktionalität ausgelegt. Dabei gibt es verschiedene Konstruktionsprinzipien, die je nach Einsatzzweck variieren. Die gängigsten Mechanismen umfassen:
- Verriegelung durch Kugeln oder Klemmbügel – Hierbei wird die Verbindung durch kleine Stahlkugeln oder einen Metallbügel gesichert, die ein ungewolltes Lösen verhindern. Sobald der Mechanismus entriegelt wird, gibt er die Kupplung frei. Diese Technik ist besonders bei Hochdrucksystemen verbreitet.
- Federmechanismus für schnelles Öffnen – Ein Federmechanismus sorgt dafür, dass der Anschluss mit minimalem Kraftaufwand getrennt werden kann. Oft reicht ein Knopfdruck oder eine kurze Drehbewegung, um die Verbindung zu lösen.
- Dichtungen für maximale Sicherheit – Spezielle Gummidichtungen oder PTFE-Dichtungen gewährleisten, dass keine Flüssigkeiten oder Gase austreten. Besonders in der Chemie- und Lebensmittelindustrie ist eine absolut dichte Verbindung essenziell.
Zusätzlich gibt es spezielle Varianten mit integrierten Ventilen, die verhindern, dass beim Trennen des Systems Flüssigkeiten oder Gase entweichen. Diese Technik ist besonders vorteilhaft bei gefährlichen oder teuren Medien, da sie Verluste minimiert und die Sicherheit erhöht.
Die Wahl des richtigen Mechanismus hängt stark von der jeweiligen Anwendung ab. Während ein einfacher Federmechanismus in der Werkstatt ausreicht, sind in Hochdrucksystemen oder sicherheitskritischen Bereichen komplexere Verriegelungssysteme erforderlich. Die Schnellkupplung ermöglicht es, Verbindungen in Sekundenbruchteilen herzustellen oder zu lösen, ohne dabei an Dichtheit oder Sicherheit einzubüßen.
Materialwahl: Kunststoff, Messing oder Edelstahl?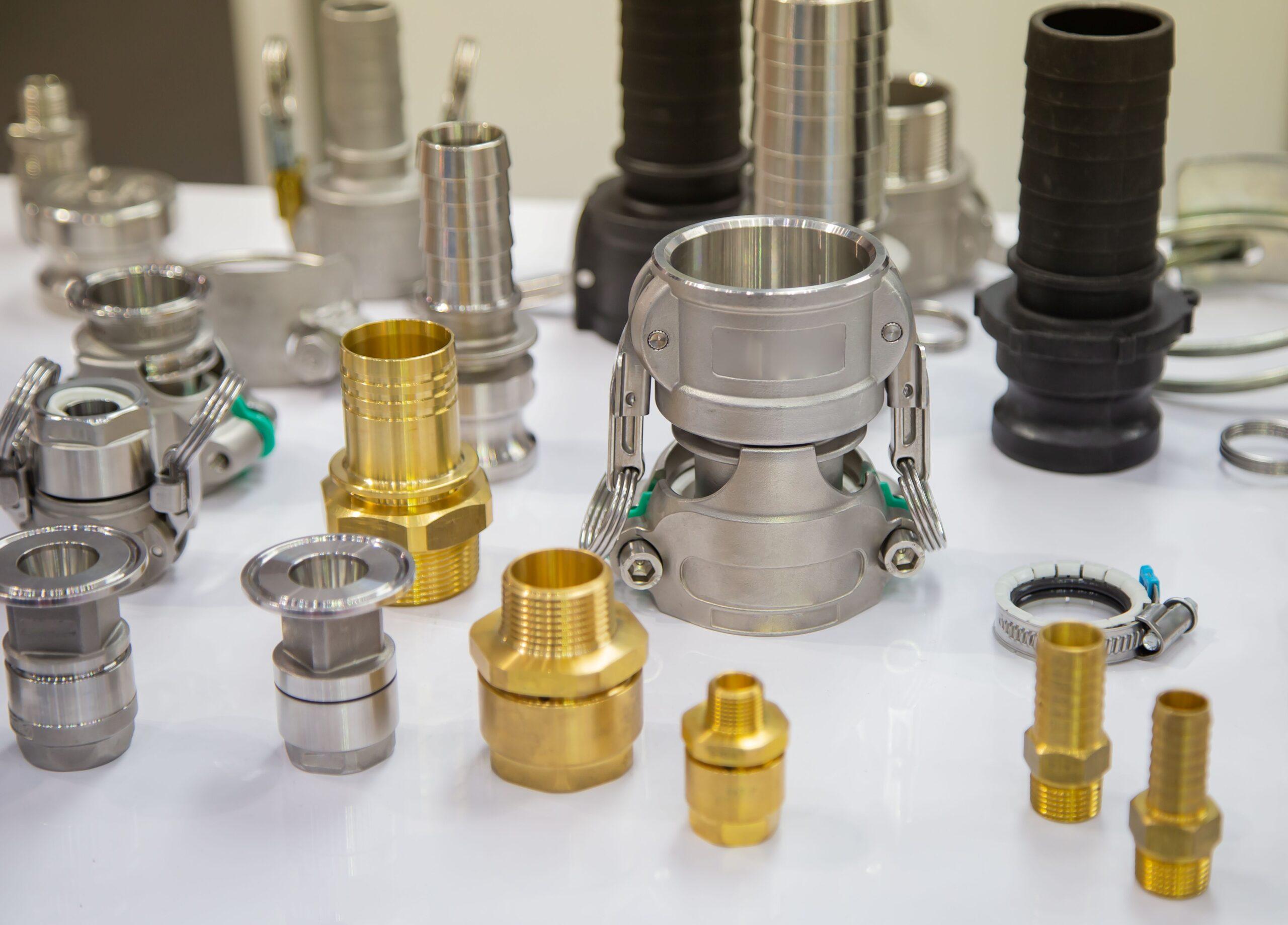
Die Materialwahl beeinflusst maßgeblich die Eigenschaften eines Anschlusssystems. Sie bestimmt, wie langlebig und widerstandsfähig ein Produkt ist und ob es für eine bestimmte Anwendung geeignet ist. Die drei am häufigsten verwendeten Materialien sind:
- Kunststoff – Kunststoffverbindungen sind besonders leicht und preisgünstig, weshalb sie häufig in weniger anspruchsvollen Anwendungen zum Einsatz kommen. Sie eignen sich für den Einsatz in der Automatisierungstechnik oder bei einfachen Flüssigkeitssystemen. Allerdings haben sie eine begrenzte Temperatur- und Druckbeständigkeit und sind weniger widerstandsfähig gegenüber aggressiven Medien.
- Messing – Messing ist eine beliebte Wahl für viele industrielle Anwendungen, da es eine hohe Korrosionsbeständigkeit bietet und mechanisch stabil ist. Es wird häufig in Druckluft- oder Heizsystemen verwendet. Der Nachteil von Messing liegt in der begrenzten Beständigkeit gegenüber stark aggressiven Medien.
- Edelstahl – Edelstahl ist das Material der Wahl, wenn es um maximale Beständigkeit geht. Es hält hohen Temperaturen, Druckbelastungen und chemisch aggressiven Substanzen stand. In der Lebensmittelindustrie, Medizintechnik oder Petrochemie ist Edelstahl oft unverzichtbar. Allerdings ist es teurer als andere Materialien.
Die Entscheidung für das richtige Material sollte immer unter Berücksichtigung der spezifischen Einsatzbedingungen getroffen werden. Wer in einem feuchten oder chemisch belasteten Umfeld arbeitet, sollte auf Edelstahl setzen, während in weniger anspruchsvollen Bereichen auch Kunststofflösungen ausreichen können.
Typische Einsatzgebiete und ihre Anforderungen
Moderne Verbindungslösungen werden in vielen Branchen eingesetzt. Je nach Anwendung gelten unterschiedliche Anforderungen:
Einsatzbereich | Anforderungen | Typisches Material |
Druckluftsysteme | Hoher Druck, schnelle Handhabung | Messing, Kunststoff |
Hydraulik | Extrem hoher Druck, Dichtheit | Edelstahl |
Chemische Industrie | Beständigkeit gegen aggressive Medien | Edelstahl, PTFE |
Lebensmittelbranche | Hygienische Standards, Korrosionsschutz | Edelstahl |
Medizintechnik | Keimfreiheit, einfache Reinigung, hohe Präzision | Edelstahl, spezielle Kunststoffe |
Je nach Branche stehen Sicherheit, Effizienz oder Materialbeständigkeit im Fokus. In sicherheitskritischen Bereichen wie der Hydraulik oder Chemieindustrie darf an der Qualität nicht gespart werden, da Fehler hier schnell gravierende Folgen haben können.
Worauf sollte man bei der Auswahl achten?
Ein hochwertiges Anschlusssystem muss mehrere Kriterien erfüllen, um in der Praxis zuverlässig zu funktionieren. Zu den wichtigsten Auswahlkriterien gehören:
✅ Kompatibilität mit bestehenden Systemen – Eine Verbindungslösung muss mit den vorhandenen Anschlüssen und Schläuchen kompatibel sein, um problemlos integriert werden zu können.
✅ Materialqualität – Das gewählte Material sollte den jeweiligen Umwelt- und Einsatzbedingungen standhalten.
✅ Druck- und Temperaturbeständigkeit – Je nach Anwendung müssen die Komponenten extremen Temperaturen oder hohen Drücken trotzen können.
✅ Einfache Handhabung – Eine intuitive und ergonomische Bedienung ist entscheidend für effiziente Arbeitsabläufe.
✅ Sicherheitsstandards – Die Verbindungstechnik muss alle relevanten Sicherheitsnormen erfüllen, insbesondere in kritischen Industrien.
Wer diese Faktoren berücksichtigt, kann Ausfälle vermeiden und langfristig von einer zuverlässigen Lösung profitieren.
Effizienz trifft Innovation
Ob in der Industrie, im Handwerk oder in spezialisierten Anwendungen – die richtige Verbindungstechnik ist entscheidend für reibungslose Prozesse. Sie sorgt für Sicherheit, spart wertvolle Zeit und minimiert den Wartungsaufwand. Moderne Systeme sind so konzipiert, dass sie eine Balance zwischen einfacher Handhabung, robuster Bauweise und hoher Sicherheit bieten. Wer auf eine durchdachte Lösung setzt, kann sich auf zuverlässige Verbindungen verlassen, die auch unter extremen Bedingungen bestehen.
Bildnachweis: Jamie Wilson, Itsanan, Titolino/ Adobe Stock